We like woodworking because it’s challenging. Sometimes an unexpected challenge rears its head mid-project, and creative problem solving is required. The tinkerer in us rejoices.
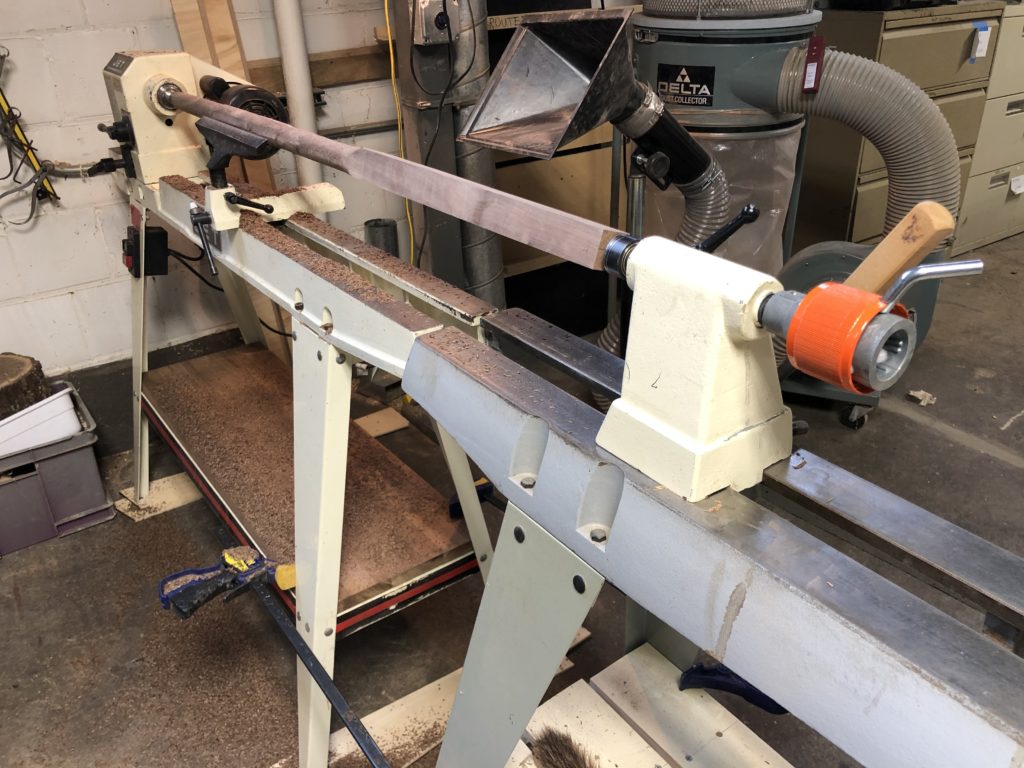
I’m working on Michael Robbins’s contemporary desk from Fine Woodworking Sep/Oct 2018 (we’ll, I’m making the base anyway). If you want to make those legs, you’re going to need a lathe. My makerspace has lathes. In my head, I check this item off as I’m preparing for the project.
Turning the legs and the side stretchers is good turning experience for me and goes relatively smoothly. The last piece to turn was the long stretcher that spans the rear legs. The stretcher is 50 inches long. To accommodate my stock, I extend the tailstock all the way to the end of the Jet lathe’s bed. To my surprise, the bed isn’t long enough. The lathe is one of the larger ones I’ve encountered, so apparently 50 inches is pretty long as far as spindles go. Time to think about options. I consider having a local shop make this part for me, but I’d have to go about finding one and potentially waiting for it to be finished. Curious, I look online for large lathes. How much would one cost? Another surprise: I never find the answer because the longest bed I could find for sale is 48 inches.
I consider making the stretcher in two pieces and joining them together with a dowel, but that isn’t aesthetically satisfactory. I talk to some people at The Bodgery. Jim, the wood shop captain, and a cabinet maker for decades, quickly rattles off four or five ideas. One of them being, “You could put two lathes together, end-to-end”. This idea immediately goes to the top of my list. The Bodgery has a Delta lathe about the same size as the Jet. Could that work? Online, I discover the bed extension, something you can make from wood and attach to the lathe when needed. But the double lathe idea would be easier and faster (if it works).
The first thing I do is take the tailstock from the Jet lathe over to the Delta to see if it fits on the bed. I’m in luck – it clamps down snugly. Then I measure the distance from each bed to the floor. The Delta is a quarter to half an inch higher – pretty close. I bring the Delta over to the Jet and put some scrap wood underneath the Jet to make it the same height. Next, I eyeball the lathes to make sure they’re aligned in a reasonably straight line. Finally, I clamp the lathes together and ready my stock for turning. I spin the stock at low speed to see what happens. I’m delighted to see that it’s turning just like it would normally.
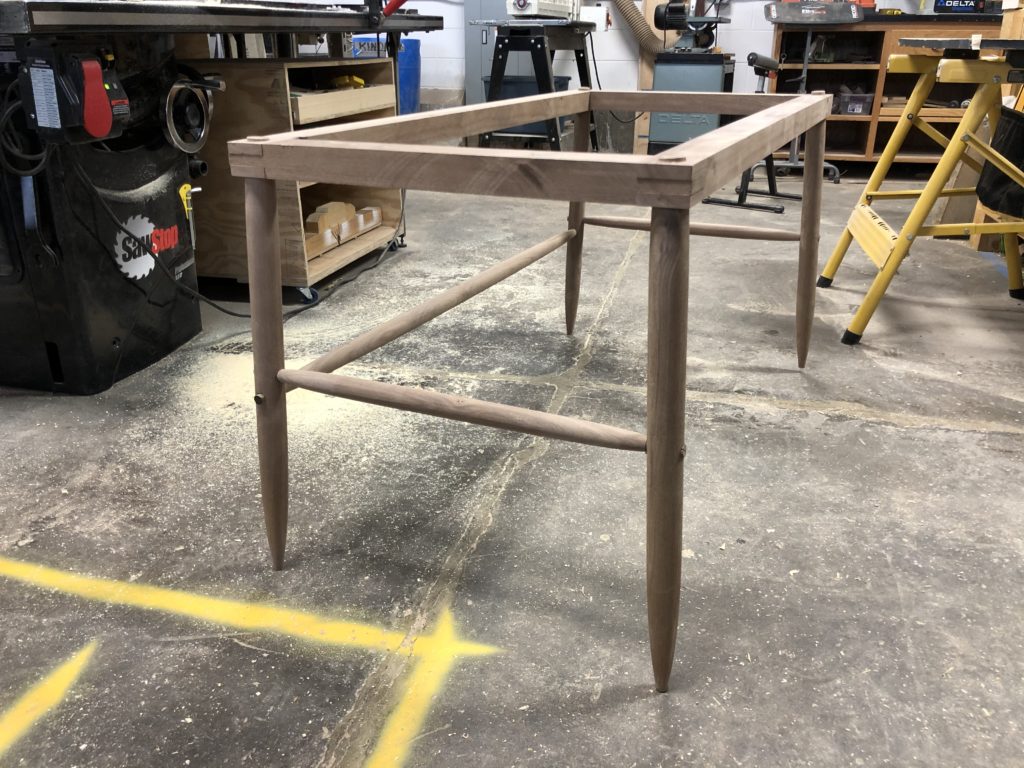
I’d say it took me at least a couple hours to turn the stretcher. But the double lathe worked like a charm. And the dry fit was a success.